Hyster® Tracker System
Save money and keep your employees safe with the Hyster® Tracker fleet tracking system. The tracking system monitors your fleet’s diagnostics, so you can provide a safe environment on the warehouse floor or out in the field. Not only does the system reduce the potential for injuries and damaged products and equipment, but it gives a high return on your investment while complying with OSHA requirements. Learn more about how the Hyster® Tracker fleet tracking system can help your company.
Three Levels of Fleet Tracking
Inside the Fleet Tracking System
-
Hour Meter Utilization
Keep a log of how much time each piece of equipment is used.
-
Impacts
Measure horizontal and vertical impacts on your machinery.
-
PM Tracker
Stay on top of material handling equipment maintenance.
-
Training Tracker
Manage necessary operator and forklift safety training for your employees.
-
Cost of Operations
Record all operations and expenses for your warehouse fleet.
-
Compliance
Abide by OSHA and other compliance laws with a touch of a button.
-
IMPACT CAMERA
Records video footage of any critical impact within your operation. -
MOBILE APP
Fleet management, operator efficiency and critical events are now at the power of your fingertips.
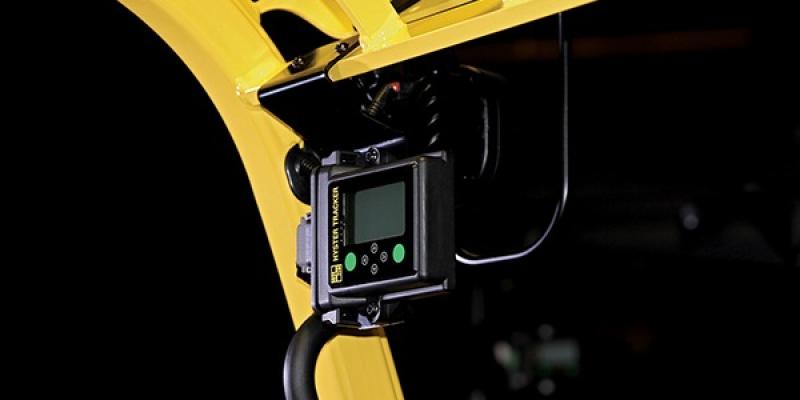
Wireless Asset Management
Promote safety in the warehouse while saving money and increasing profits with the Hyster® Tracker fleet management software. With tools like fleet tracking, GPS, and fault code tracking, the Hyster® Tracker system is essential for any fleet management effort. The fleet tracking program also keeps track of spend by location so you can efficiently manage projects in several cities and counties from wherever you are. Learn more about what the Hyster® Tracker fleet tracking system can do for you.
Why Choose a Hyster® Tracker System?
Watch your operating costs diminish with the Hyster® Tracker fleet management program. From reducing equipment, property, and product damage to avoiding bills due to damage and injury, you will see the difference with a Hyster® Tracker in no time, not to mention reducing spend on material with the program’s wireless and paperless options. Talk with a knowledgeable Papé Material Handling employee more about installing Hyster® Tracker software for your fleet to start saving time and money.
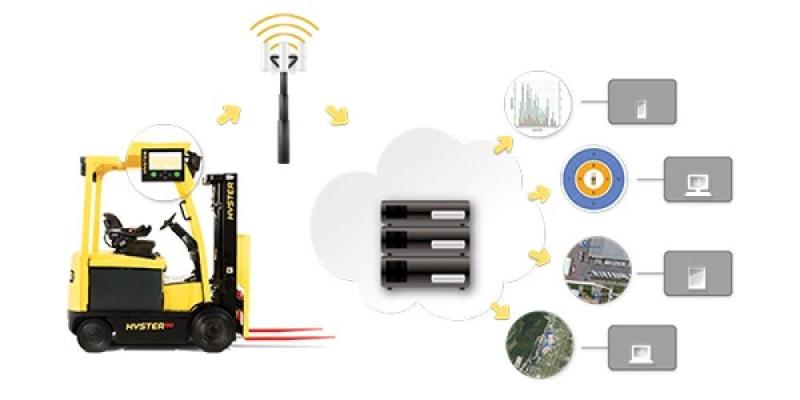

Battery Tracker
Don’t let your warehouse fleet die on you while on the job. With Hyster® and Yale® battery trackers, be in the know when your fleet is running low on power. The six-step process is made simple so you can implement battery trackers on your fleet effortlessly. Additionally, you can track all your material handling equipment’s batteries online, so you can check in on your fleet at any time from anywhere. Learn more about how to install Hyster® and Yale® battery trackers on your fleet.